News & Notes Archive - October 2008
Troubled big banks may grab the headlines but the good news for home buyers is there are plenty of healthy local and regional banks and credit unions willing to lend. Some tips when shopping for a loan.
In chapter 4 of the Buyer’s Guide—“Getting started, calculating your buying power”—I advise home shoppers to shop for the money first, and where possible, get a pre-approved loan before beginning a home search in earnest. I also suggest the best place to start is with your local bank or credit union. This recommendation still holds even during this time of economic upheaval when major banks are seeking government bail out funds to survive. Here’s why:
The principal cause of the financial industry’s meltdown this year has been the high levels of toxic securities (i.e. stocks and shares) that big banks purchased in recent years, consisting of bundled subprime home mortgages that have proved all but worthless. But what is less well known is that there are literally thousands of small community banks that were never tempted to buy any of these high-flying offerings, and they have been doing just fine, thank you very much.
These banks have money to lend, and by golly they’re lending it. Currently a lot of their loans are to homeowners refinancing their mortgages to take advantage of the historically low interest rates. But there’s also money for first time homebuyers, even for those seeking personal property loans (i.e., chattel loans) for new manufactured homes that will be sited in land-lease communities (mobile home parks). The key is to have good credit. If you have a credit score of 700 or better, you should have little difficulty, although if your current job is in an industry being hit hard by the recession, you may encounter additional requirements to assure the lender you can cover the payments. At present the average credit score of residents of leasehold communities is in the 660 range. Parenthetically, I have heard reports that the default rate of residents with scores around 650 is close to 50%. This is troubling. But that’s another story.
Here are a few tips for loan shopping:
- Start with the bank where you keep your savings and do your banking. The loan officer there will have a record of your account activity and you will start off with a built-in comfort level that will be in your favor.
- Consider as well your local/regional credit union. If you don’t have an account there, you can open one. Credit unions are not-for-profit enterprises and they often have very competitive rates. And like banks, they’re local. If you run into a financial rough patch, you’ll have someone there you can personally work with, not an impersonal voice hundreds of miles away.
- If you’re looking for a loan from a source outside of your region, I often recommend to my clients CU Factory Built Lending. This is a division of the San Antonio Credit Union that lends specifically to the manufactured home sector (including chattel loans). Call SACU toll-free at 800-234-SACU. On the web, go to www.sacu.com/MenuLoans/MfgHomeLoans.asp Alternatively, go to www.sacu.com, select “loans” from the menu on the top, and mouse down to “manufactured homes.” You’ll find there the telephone number for the office in your region.
- Be informed about the $7,5000 tax credit for first-time homebuyers. If you haven’t owned a home for two years, you qualify as a first-timer. This credit can often be used toward a down payment. See September 2008 News & Notes for details. This is good news, indeed.
Interview: 15 minutes with...Emanuel Levy
Note: In my role as an industry observer and consumer advocate I speak with people at all levels of the manufactured home industry (MH) to gain insights I share with my readers to help them be better informed. Some I have interviewed for a one-page column that runs in an industry trade publication. In return the magazine runs an ad for the Grissim Guides. No money changes hands. I insist on this. Aside from book sales, I neither solicit nor accept a dime from the industry, and my readers have my assurance I intend to keep it that way. Here’s this month’s interview:
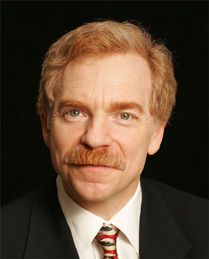
Emanuel Levy, Executive Director, Manufactured Housing Research Alliance
Who: Executive Director, Manufactured Housing Research Alliance, based in New York, NY
Background: Age, 56. Born 1952 in Ravena, NY (upstate), the youngest of three children. Both parents were in the garment business, operating a blouse manufacturing plant until the demise of garment manufacturing in the Northeast (“Experiencing first-hand an industry downturn at the age of 10 left an impression.”) His family relocated to New York City in ’62. Levy attended Syracuse University (Syracuse, NY) completing a 5-year architectural degree in ’75, followed by an additional year at Carnegie-Mellon University (Pittsburg, PA) earning a Masters degree in Architecture.
Returning to New York City, he spent two years working for renowned architect Richard Stein, an early pioneer in energy and sustainable building. “Dick would approach the design of buildings with an understanding of environmental impacts that we are struggling to achieve today.” In ’78, Levy moved to a building systems consulting firm, his indoctrination into the world of HUD-code and modular housing. He remained there five years leading a group that worked on a wide range of cutting edge energy projects for public and private organizations, including the American Institute of Architects, the DOE and HUD.
In ’83 Levy left to form his own company, The Levy Partnership (TLP) and gravitated toward work in the building systems field. MHI was a mainstay client. TLP grew a diverse client base of private sector, institutional, as well as government clients. An early project provided the basis for a program that would eventually become the Super Good Cents Manufactured Housing program in the Northwest. Levy also began working with the electrical utility industry, particularly companies in the Southeast that were attempting to promote efficiency for their customers living in manufactured homes. Seeing the value of having several utilities with contiguous service areas cooperate on a common program, Levy became a central player in forming a jointly-funded, non-profit research group called the Southeast Manufactured Home Alliance. Levy was asked to serve as executive director. By 2000, with the factory built industry now fully involved through MHI, the organization morphed into the Manufactured Housing Research Alliance with a broad research agenda and national scope. Levy has received numerous industry awards, including the MHI Chairman’s Award, the Frank Walter Standards Award and the Progressive Architecture Award. Levy’s wife Cindy is a professor at Hofstra University where she teaches theatre and chairs the Women’s Studies Department. The couple have two girls, Anya, 18 and Adin, 13.
- Q: How many members does the MHRA have? Its staffing and budget?
- A: We have between 300 and 400 members, although the number of companies and organizations we work with is much larger. Companies joining MHI receive membership in the Alliance as a benefit. Members contribute about $150,000 annually, an investment that we use to attract matching funds for projects. Currently we have ten people on staff, with an yearly budget of $1.5 million.
- Q: For an industry so fiercely competitive, it’s pretty amazing to see companies collaborating so well together.
- A: Exactly. The idea is, initially, counterintuitive. Competition turns into “co-opetition.” The genius of the Alliance is it allows projects to be directed by committees of industry people who outside the tent fiercely compete, but under the research tent work together for common gain. The result has been an extraordinary success record that has transformed aspects of the business. A recent report by the National Academy of Sciences included an assessment of research conducted by MHRA for HUD noting that “the modest funding (provided by HUD to MHRA) resulted not only in producing tangible products, but also in improving an entire industry that provides an important source of affordable housing.”
- Q: Some recent examples?
- A: The Energy Star programs for manufactured and modular homes, introducing lean production methods to the industry, studies on moisture mitigation and the Model Installation Manual are high on the list. But some of the small focused technical studies demonstrating, for example, that manufactured homes have low levels of indoor air pollutants like formaldehyde or perform well when exposed to hurricane conditions, are a critically needed response to widely held public misperceptions.
- Q: What’s got you excited?
- A: A lot, and a lot’s happening. Topping the list are environmental initiatives, including Green and sustainable design, continuing emphasis on energy efficiency, and indoor air quality. My guess is in the next several years we’ll be developing economically-viable net zero energy homes and casually using terms like “carbon footprint.” Also poised for equally profound changes is the whole area of home installation and foundation design; this at a time when homes are becoming increasingly more complex and home site completions more elaborate. Increasingly, our industry will benefit from tools that integrate the whole process of building, delivering and installing homes in a more transparent and foolproof manner. Helping to improve the sales and installation process is one of our holy grails.
- Here’s an issue dear to my heart: are there alternatives for building HUD code homes that would eliminate the I-beam chassis, allowing homes to more easily be placed on permanent foundations or used for two-story designs? No question that the entire floor system is ready for an overhaul. We are using a last century design for the part of the home that forms the junction of nearly all of the building systems, must function as an effective thermal and moisture barrier and the structural platform for the home, attaches to a transportation system and is the interface with the site built features. It’s a challenge worthy of joint support. I’m sure we can do better.
- Q: Does MHRA emphasize research on any one aspect of factory built housing?
- A: Not really, but all Alliance research shares three qualities: one, the benefits for factory building are obvious and tangible (although not always measurable); two, the results manifestly improve the value and performance of the products our industry provides; and three, the research has broad appeal potentially providing benefits to a large cross section of the membership. Technological innovation, new building systems, energy efficiency, process improvements, market studies, building science studies: they’re all on the table.