Notes Archive - February 2007
With no warning Georgia builder General Manufactured Housing closes. Chicken-hearted behavior of company management a black mark on MH industry.
When employees of the Waycross, GA-based MH builder General Manufactured Housing showed up for work on Tuesday morning, January 30th, they were shocked to be told they were being laid off immediately and that the plant would be closing permanently. The Waycross Journal Herald reported no plant officials were available for explanation or comment and calls to the plant were not answered.
The announcement came as a complete surprise to the nearly 200 factory employees as well as officials of the Georgia Department of Labor who rushed to the scene to offer help with state-sponsored assistance programs. One state official told the Journal “We were shocked. We were out there Monday and no one said a word.”
Calls in late February to GA retailers of the privately held company’s homes yielded no details as to why the factory closed, although speculation was “the bank shut them down.” The sales manager of one retailer, Brunswick Homes, in Brunswick, GA, said he had been very happy with the builder’s products and service—“good people to work with.” In The Grissim Ratings Guide the company received a construction rating of 4 —below average.
My comment: In an uncertain business climate it is not unusual for factories to close abruptly, but the utter failure of senior management of General Housing to make any effort to offer an explanation to the employees and their families, or to offer help with the transition, let alone refusing to answer the phone, is uncaring, unethical, cowardly, grossly irresponsible and shameful. Regrettably, this kind of cynical no-compassion/ no guts behavior only perpetuates the tarnished image of an industry that deserves better.
Photos of the HUDdled masses in Hope, Arkansas. FEMA officials, citing many homes are water damaged, ask builders for repairs. Builders to FEMA: “Sorry, Charlie”
In my May 2006 News & Notes, I reported that, following Hurricane Katrina (which struck the Gulf Coast region in August, 2005), FEMA purchased 24,967 manufactured homes at a cost of $862 million, and 1,755 modular homes at a total of $52.4 million. Close to 60 percent of these homes had not been deployed to the Gulf region and probably won’t be. “Deployed” does not mean the home would ever be lived in, only trucked to one of 11 staging areas.
The largest of those staging areas is Hope, Arkansas, where more than 10,000 singlewide homes are stored. Witnesses who have flown over the Hope staging area say the sheer size of the huddled HUD-code homes is breathtaking. Check out these photos recently taken by an industry source.
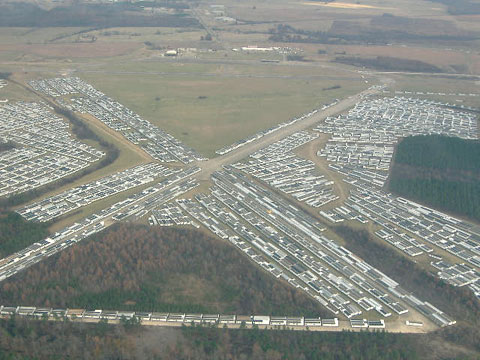
X marks the spot, and probably easily seen from space
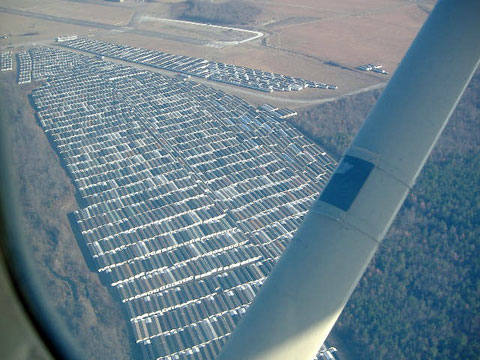
If neatness counts, the folks who told the delivery tractors where to park their cargo deserve high marks.
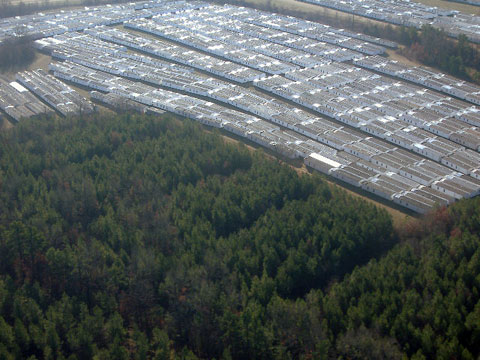
Your government at work: When the Inspector General for the Dept. of Homeland Security investigated the decision making process after Katrina, the IG was unable “to identify the FEMA official(s) who authorized the purchase of manufactured home.”
Heck of a job, Brownie.
Earlier this month FEMA officials released inspection results that showed hundreds of these cheaply constructed temporary homes had sustained water damage, largely due to moisture getting inside through the soffit vents, ridge vents and gable vents. They sent urgent emails to the MH builders to contact them immediately to arrange for repairs.
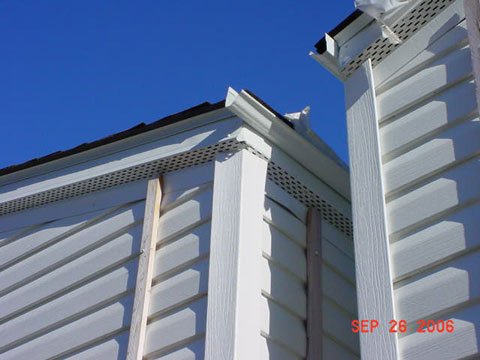
These soffit vents are perforated strips under the eves that allow air (and moisture) to circulate in and out of the attic space.
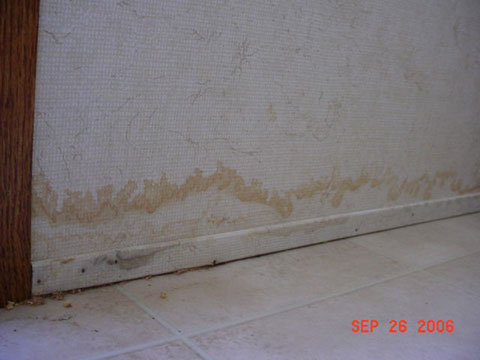
Water damage to flimsy wallboard, perhaps from water seepage through cracks in the roof and walls due to little or no blocking the prevent sagging.
The builders replied in effect, “No way,” refusing any service repairs, saying it was FEMA’s responsibility to properly block the homes in storage to ensure watertight integrity. Absent FEMA coming up with any legal contract obligating the MH builders, it’s doubtful the agency can force the builders to comply. Heck, FEMA can’t even find who okayed the purchase of the homes in the first place. Heck of a job, Brownie.
Manufactured housing’s grim forecast for 2007 holds silver lining for MH home buyers.
Last year manufactured housing’s shipment levels were a dismal 118,000 homes nationally, the worst since 1961, with expectations that 2007 may trend downward to around 100,000. As a result many of the factories of the nation’s 83 builders are running at half or less capacity, with several experiencing idle days regularly for lack of orders.
The good news for MH home buyers is that with factory backlogs currently very low—on average a week or less—home buyers can anticipate that their ordered homes will be quickly manufactured, with deliveries to a site comfortably under 30 days from the placement of the order.
Interview: 15 minutes with...Jennifer Hall
Note: In my role as an industry observer and consumer advocate I speak with people at all levels of the manufactured home industry (MH) to gain insights I share with my readers to help them be better informed. Some I have interviewed for a one-page column that runs in an industry trade publication. In return the magazine runs an ad for the Grissim Guides. No money changes hands. I insist on this. Aside from book sales, I neither solicit nor accept a dime from the industry, and my readers have my assurance I intend to keep it that way. Here’s this month’s interview:
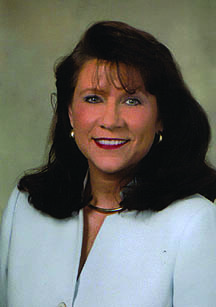
Jennifer Hall, Executive Director, Mississippi Manufactured Housing Association
Who: Executive Director, Mississippi Manufactured Housing Association
Background: Born and raised in Fulton, MS, in the rural hills of northeast MS, 18 miles east of Tupelo (Elvis’ birth place), “a small, close-knit town—my father and mother still live in the house we four children were raised.” Attended Atawamba Agricultural High School, then to Mississippi State University, graduating in ’81 with a BS in business. Briefly managed a women’s apparel store, married, then took six years off to raise a son and a daughter, “but found time to get involved in politics, helping with Trent Lott’s successful ’88 campaign for the U.S. Senate—“The man is extremely intelligent and well-versed, a bull dog personality but he’s very charismatic and gets along with a lot of people.” Returning to the career track, developed a music program for a private Christian school, then for two years (’91-’92) served as director of the Main Street Program for Columbus, MS, a joint Federal, State and city revitalization program. In ’94 recruited to move to Jackson to become finance director of Friends of Kirk Fordice, a fund-raising effort to re-elect then governor Fordice, the state’s first Republican leader. Traveled extensively throughout the state with the governor, raised $4 million for a successful ’95 re-election campaign. “The most demanding job I’ve ever had but it was also the most exciting.”
In ’95, at the urging of a friend she’d met during the campaign who owned an MH dealership, she interviewed for the executive director position at the MS Manufactured Housing Assoc. “At the time I knew nothing about the industry, I just thought of them as house trailers.” But her unsurpassed political connections, many on a first-name basis, landed her the job. “First thing I did was tour four plants, hard hat and safety glasses and all, to learn everything I could, from blue prints to the production line, to see for myself how they were made.” In the 11 years since then, actively promoted networking among all segments of the building industry. In the aftermath of Hurricane Katrina, played a key leadership role in organizing aid and reconstruction efforts. In 2005 voted one of the Top 50 Women in the state of Mississippi (that same year she was voted MHI’s Executive Director of the Year). Her husband Richard Hall is a transportation commissioner. The couple have four children and two grandchildren.
- Q: You’ve joked that 18 months after Hurricane Katrina you’re still in the middle of the storm. What’s the latest?
- A: In Mississippi at the end of 2006 there were still over 92,000 people living in temporary housing. That was made up of 30,000 travel trailers and about 5,000 manufactured homes, most all single-sections. It’s been a disappointment that more manufactured homes weren’t sited but local governments have held up approvals out of fear of creating FEMAvilles. But as the rebuilding has finally begun in earnest, and HUD-code homes have become a huge part of the mix: last year they were 35.8% of all new home starts, mostly on the coast. That’s one out of every three homes since January, 2006.
- Q: The Mississippi MH industry helped produce a rebuild-the-coast conference in Hattiesburg just ten weeks after Katrina. How did that go?
- A: Really well. Hattiesburg is 60 miles from the coast and about 50,000 Katrina survivors had moved to the area and hotels were packed, but there was tremendous interest from developers and contractors, everyone in the housing industry, and we saw an opportunity to showcase factory built homes. On short notice we set up an Oak Creek modular model and a Cavalier three-section HUD code home. We expected maybe two- to three-hundred but over six hundred showed: government and non-profit agencies, builders, realtors, developers, a big cross section. Then, four months later, at the South Central industry show in Tunica, a big effort was made to invite coastal mayors and supervisors to the show and inspect the model homes. Over 130 elected officials showed up. I was thrilled.
- Q: Some builders, such as Palm Harbor, are focusing on modular homes because they don’t have to fight the zoning restrictions in many areas of the coast. Your thoughts?
- A: That’s true, but the cheapest modular home I have been able to find on the coast, 1100 square feet, delivered and set up, is $103,000. That’s still not affordable for a lot of people who lost homes, many who don’t have insurance. We’re talking about 70,000 homes lost or severely damaged in a six county area, so there will be great opportunities for homes of both codes. The public clearly wants to know more about factory built housing. Our association is putting together an Affordable Housing Initiative on the coast that will be a major public education campaign.
- Q: Are you running into the “looks like a mobile home” stigma?
- A: There is some of that, to be sure, but what’s exciting is the great new home designs that we’re seeing from builders like Patriot, Palm Harbor and others that give HUD code homes great curb appeal. Many of the manufacturers developed cottage models and displayed them at the August Governor’s Recovery Expo. Florida architect Steve Mauzon who works with a group called New Urbanism helped create a pattern book with elevations and designs for homes that are beautiful. Steve’s from outside our industry but he’s a great believer in MH. He said “You don’t have to convince me that manufactured housing is safe housing. You’re building a great product. It’s almost there, but it looks like crap. And there’s no reason why. For starters, put on a front porch.” Last March I invited Steve to Tunica to show his pattern book to manufacturers. But, to be honest, we still have manufacturers who say “This is my product; it should be enough for people who need housing, take it or leave it.” As long as they’re making money, they see no reason to change. And that’s the biggest thing that upsets me. Builders with that attitude are missing the boat.
- Q: What’s got you most excited about the post-Katrina rebuilding effort?
- A: Katrina has provided an incredible opportunity for our industry to step forward and create, design and build quality homes, both HUD and modular, with tremendous curb appeal, and that could change the face of our industry. Literally. I have thought that from day one. Our Coast residents need affordable, quality housing and I believe our industry can deliver a superb product.