Notes Archive - January 2007
With some MH builders struggling, beware of factory-direct back door sales deals
As the Grissim 2007 Report describes, many MH builders are going into this year on the endangered list. With only around 120,000 homes were sold last year, some factories, desperate to keep their production lines going, are cutting deals with home shoppers who visit for factory tours, agreeing to build and ship a home directly to the customer’s site without the participation of a local dealer or a general contractor well-known to the factory. These transactions, with no oversight is a recipe that can lead to disaster.
I’ve heard of two instances here in the Pacific Northwest. In one case the home was delivered to land for which no permits had been given, no septic system approved or installed, and no foundation constructed. Wet weather caused the parked sections of the home to sink in the mud. When a Cat was brought in to pull them free, it, too, became mired. A second and larger Cat had to be brought in to complete the rescue, at considerable expense. During the set up, installers found the tape and texture was the wrong color and so poorly sprayed on that it had to be re-done, causing further delays. A second home, from another builder, was shipped to an elderly widow whose site was similarly unprepared, and the MH builder said there was no warranty in force because the home had not been purchased through a dealer. I’ll be looking into these stories and will be reporting any additional findings here.
Please see my October 2006 News & Notes for further details about these dubious back door deals that can trap consumers in a morass of expensive trouble.
Tape and texture is a good option, but is it actually paint? Well, yes and no....
In the Grissim Guides, and at many retailer sales lots, you’ll hear talk of tape and texture for the dry wall interior walls of a new home. This is a good option and I recommend buyer’s order it. At the factory the dry wall sections are taped over at the seams and sprayed with a combination of plaster (“mud”) mixed with a primer paint, usually generic off-white color. Once the home is on-site (this applies to multi-sections, not single-wides) installers will apply an additional finish coat of primer to help disguise the marriage line and other scars associated with assembly of the home’s sections.
The textured walls look fine. But is it paint? Not really. It’s water soluble latex primer, and it will last awhile, but if you try to clean, say, fingerprints off the surface with a sponge or cleanser, the primer will come off, leaving a gray discoloration beneath. Many homeowners discover this only after several years in their new homes, especially in their kitchens and bathrooms where high moisture and water splashes take their toll. Very few dealers will disclose this information.
Recommended: When your home is being installed, hire a painter to paint at least the kitchen and bathrooms with water resistant latex acrylic paint (you can buy the paint yourself at a home improvement store). If you can afford to, have the entire inside painted. It’s not that expensive, can efficiently be done during set up, and is a sound investment in your home’s long term resale value. Plus, you can choose color schemes other than bland off-white.
Interview: 15 minutes with...Tony Lucas
Note: In my role as an industry observer and consumer advocate I speak with people at all levels of the manufactured home industry (MH) to gain insights I share with my readers to help them be better informed. Some I have interviewed for a one-page column that runs in an industry trade publication. In return the magazine runs an ad for the Grissim Guides. No money changes hands. I insist on this. Aside from book sales, I neither solicit nor accept a dime from the industry, and my readers have my assurance I intend to keep it that way. Here’s this month’s interview:
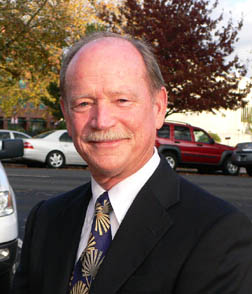
Tony Lucas
Background: Age 59. Born, raised and schooled in Salt Lake City, UT, attending U. of Utah for a year (1966), then joined his parents who had earlier relocated to San Francisco, at that time the epicenter of the Sixties–“From one cultural extreme to the other [laughs], a shock of a magnitude I’d never before experienced.” Briefly studied architecture at College of San Mateo before enlisting in the Air Force in ’67. High test scores lead to a posting at the then-ultra-secret National Security Agency in MD where he met his future wife, Jan. Completing military service in 71, returned to CA, continued architectural studies at U. of CA (Davis), graduated in ’75 (BA, political science) and began his career as an engineering draftsman for International Modular in nearby Woodland, CA. A year later Fleetwood recruited him to help them transition to the new HUD code, then promoted him to quality control manager. In ’77 he moved to Silvercrest’s Woodland plant (foreman of off-line stations), then a year later moved to The Dalles, OR for a two year stint as production mgr. for Fuhrman Homes/Global Housing (mod and HUD homes).
By 1979 he returned to Silvercrest, this time as engineering manager of the builder’s two OR plants, then as a designer, beginning a 20-year association during which his award-winning design concepts–e.g., open sight lines, angled walls, high ceilings, large windows, reflecting both a California openness and a Southwest flair–were hugely successful and widely emulated. During the mid-80s, briefly free-lanced as an architectural consultant (clients included Moduline, Golden West, Marlette, High Chaparral as well as Silvercrest) before returning to consult exclusively for Silvercrest. Along the way, earned an MBA and a law degree (the latter from Williamette U., ‘88), began a law practice in Salem, OR in ’92 with a partner, specializing in MH law. In ’99, accepted an offer from Patriot to redesign many of their product lines, moving to Elkhart, IN. By 2003, having completed that task, signed on with Palm Harbor (relocating to Dallas, TX) as VP of Design and product development, focusing on modular homes (he designed and developed PH’s stand-out Discovery Series. The Lucases have two daughters, Holly, 34 and Amanda, 24.
- Q: For the past two decades you have arguably been the industry’s premier designer. A Tony Lucas home carries a hallmark cachet and a distinctive look. How did that evolve?
- A: In the early 80s Silvercrest’s Oregon plants were building homes mostly for private properties, so being free of the design constraints common to most land-lease communities encouraged my creativity, as did Silvercrest. Plus, I’ve always loved architectural history. It moves through time like a slow stream, representing consistencies that have always appealed to people. I’ve always tried to design homes that generate in people a certain sensitivity to those elements. People may not recognize them but emotionally they do.
- Q: You almost single-handedly introduced “front porch Americana” to the industry.
- A: That was in part my response from reading articles about the sense of alienation many Americans were feeling. Around that time I was looking at land-lease communities in Michigan and to my astonishment, nobody was building homes specifically designed for communities. The homes had no aesthetics. The utility doors opened on to the streets. There were no elevations. Very ugly. So I began designing homes with end entries and porches. At first the manufacturers resisted. They were especially resistant to building porches. But, working with Patriot at that time, I took the concept to Louisville and talked to a lot of builders, developers and community owners, and that led to a whole line of Patriot homes that worked its way into Texas.
- Q: With Palm Harbor you’ve jumped right into the post-Katrina rebuilding effort, principally on the modular side. How’s that going?
- A: Really well. Things were slow at first but they’re starting to pick up. Because almost all the areas needing replacement homes are zoned for stick-built or modular, not HUD, Palm Harbor has focused on presenting modular products, including two of my designs, the Magnolia and the Azalea, that embody the character of traditional Gulf Coast homes. Actually, the concept for the Magnolia was pre-Katrina, designed as a home on stilts for the Gulf shoreline, but now that FEMA has ruled that most all replacement homes in the affected parishes must be at least five feet above their foundations, many builders are bumping the height another three to four feet and putting in garages.
- Q: Modulars are a real challenge to many traditional HUD builders. They’re more complex and demand a higher factory skill level to build. As much as 25% of their construction is done on site, and it takes time for the general contractors to get up to speed. You’re thoughts?
- A: I agree. And the industry knows this. What I’m seeing is a transition to building a product that the public generally would accept as mainstream housing. And not all of the HUD builders will make that step successfully. What Palm Harbor is doing is developing techniques that allow us to successfully build quality modulars in plants that historically have done HUD only. And I believe our success will help influence other companies to make the same decision. As builders become accustomed to building modulars and get a few successes under their belt, they’ll take that knowledge and put it into their HUD product, bringing its quality up to that of mainstream homes.
- Q: Will partnerships with developers be a large part of that matrix?
- A: Absolutely. Palm Harbor is being courted by some of the bigger builders in the U.S. who are desperately in need of high quality, well-built homes, but they can’t find the skilled labor force. Plus, they see a huge time savings with factory-built. And some of these are homes in large upscale subdivisions that will retail in the $800,000 to $1,000,00 range. So, to sum it up, if this positive movement persists for any length of time, this industry will never be what it once was. It will have evolved into a more fruitful environment–the mainstream housing universe.